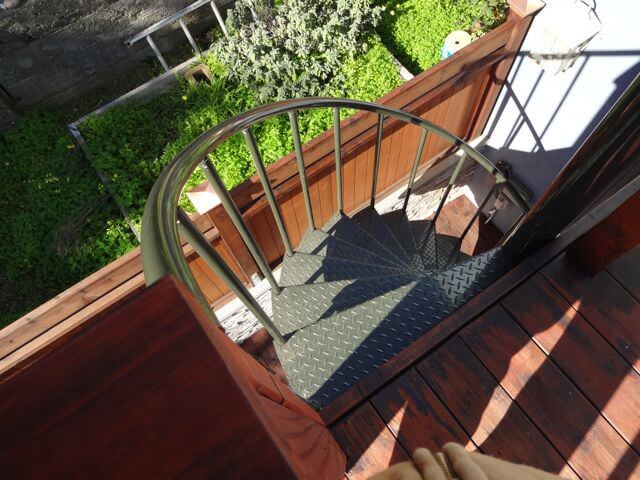
Completed Project: Noe Valley Makeover 2013
Below is a photo of a rear yard in Noe Valley. We installed the lower deck and fences about 6 months ago and soon we’ll be going back to finish the landscaping. Included in the project will be a patio, stone planters, water feature, spiral stairs, curved bench/pergola, lighting, plants etc.